Contract Manufacturing – Value Added Services
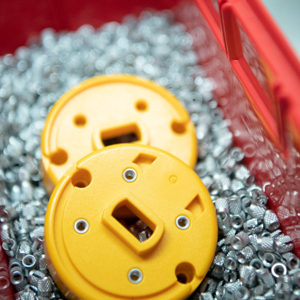
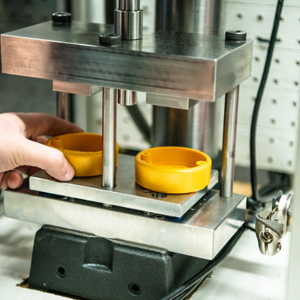
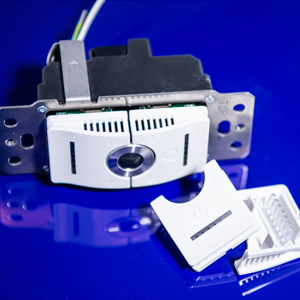
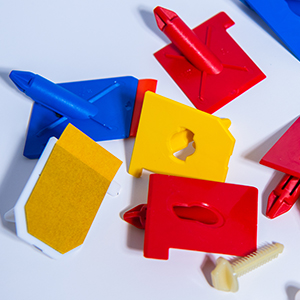
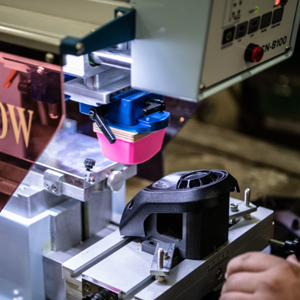
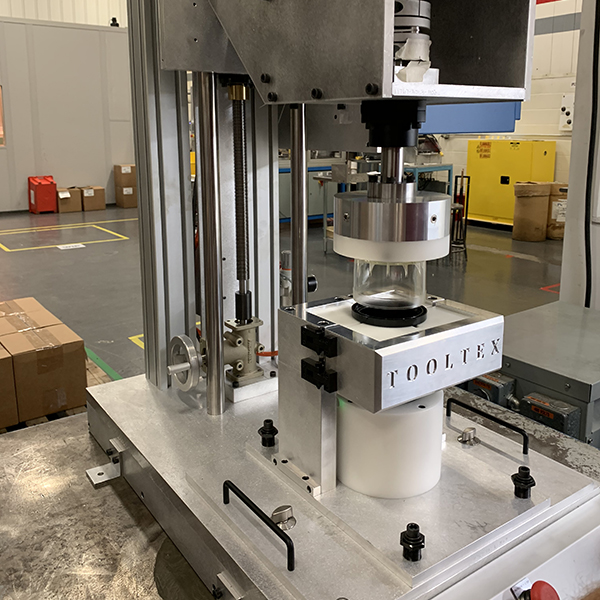
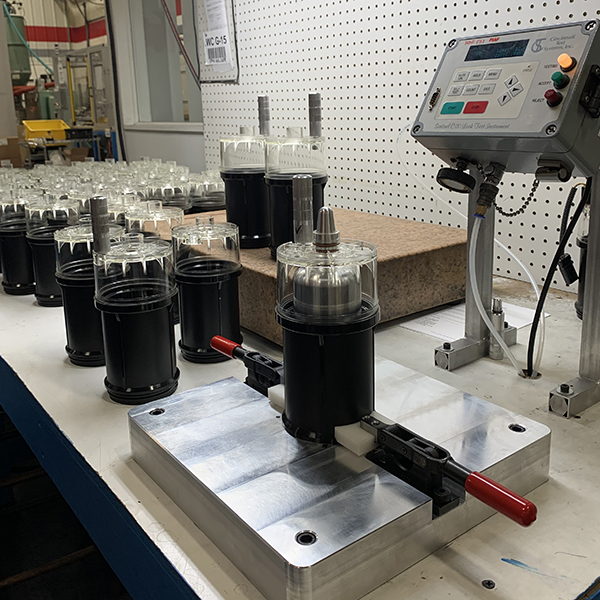
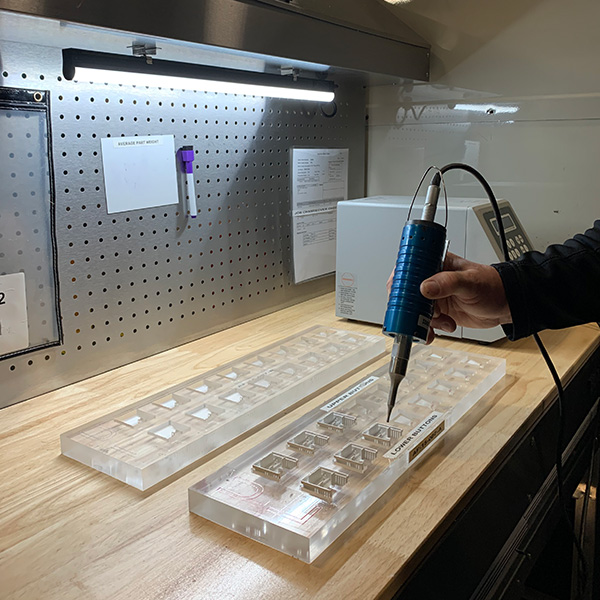
Pleasant Precision employs highly skilled team members, trained and prepared to meet market needs. We utilize electric injection molding machines and a class 100,000 cleanroom with an IATF 16949: 2016 Certified Quality Management System. Our presses can handle jobs that require clamp force in the range of 55 to 400 tons. We also offer secondary operations including assembly, pad printing, kitting, heat staking, application of pressure-sensitive tape and other value-added processes.
When we launch new products and programs at PPI, our cross-functional team goes through a series of pre-established checklists that ensure an exceptional launch. We use a detailed 8-point process to follow each product from concept to the design phase, through to production and support after the sale. To review our proven process click here.
IATF 16949: 2016 Certified QMS
- Advanced Product Quality Planning (APQP)
- Production Part Approval Process (PPAP)
- Initial Sample Inspection Report (ISIR)
- IQ, OQ, PQ Validation Protocol
- Certificate of Compliance
- Calibration Records
- Gage R&R
- UL Certified Parts Fabricator

Reduce your product costs!
The 6M’s of Manufacturing can help reduce your costs.
Get the FREE guide!